Test and measurement equipment plays a crucial role in various industries, facilitating research, development, and quality assurance processes. Over the years, these instruments have undergone significant transformations, evolving from analog to digital technology.
This revolution has brought about substantial improvements in accuracy, efficiency, and data processing capabilities, making modern test equipment indispensable in today’s technologically advanced world.
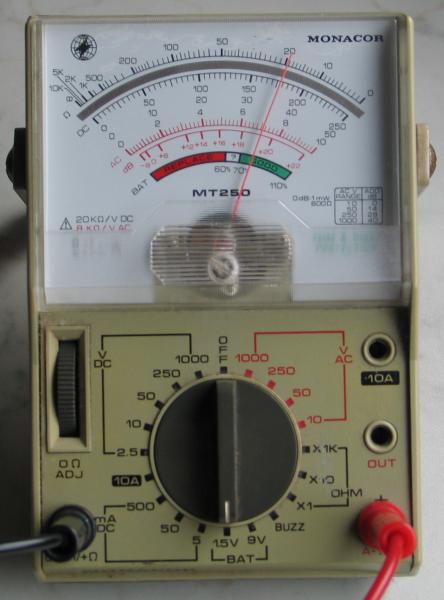
The Analog Era
In the early days of test and measurement, analog instruments reigned supreme. Engineers and researchers relied on devices such as analog oscilloscopes, function generators, and multimeters to carry out measurements. These analog instruments operated on the principles of electrical currents and voltages, providing valuable insights into circuit behavior and signal characteristics.
However, analog instruments had their limitations. They were susceptible to noise, resulting in less precise measurements. Calibration was also a challenge due to the drift in accuracy over time. As technology advanced and the need for more precise measurements arose, the limitations of analog instruments became evident.
The Rise of Digital Technology
The advent of digital technology marked a paradigm shift in the test and measurement industry. Digital instruments began to replace their analog counterparts, offering distinct advantages. Digital oscilloscopes, for instance, provided higher bandwidths, faster sampling rates, and better signal visualization. Digital function generators allowed for precise frequency control and the generation of complex waveforms.
One of the key benefits of digital technology was the improved accuracy and stability of measurements. Unlike analog instruments, digital devices quantized signals into discrete values, reducing errors and noise susceptibility. Additionally, digital instruments provided better resolution, enabling engineers to capture fine details in signals.
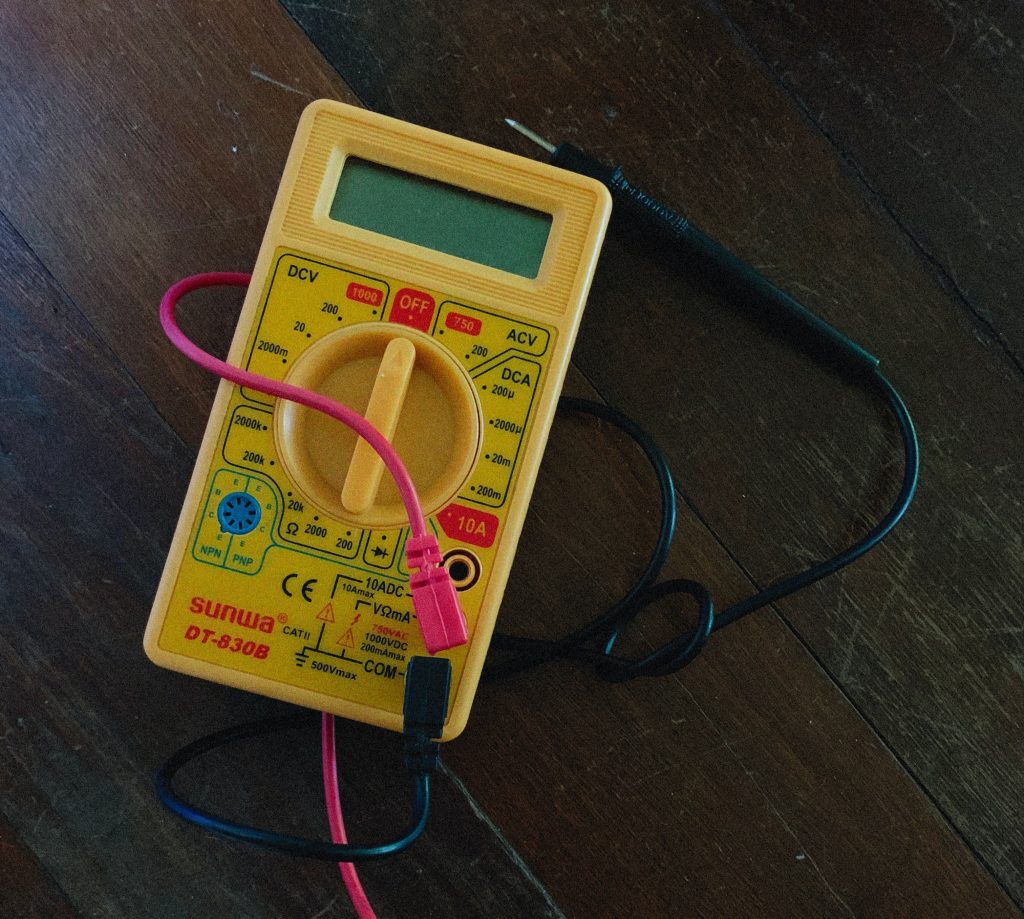
The introduction of digital instruments revolutionized the test and measurement industry. Engineers and researchers could now rely on more accurate data, leading to improved product designs and faster development cycles. Digital instruments paved the way for greater automation, making testing processes more efficient and repeatable. Moreover, digital technology brought software-defined instruments, allowing for enhanced flexibility and customization. Engineers could now tailor their measurement setups to specific needs, adapt to changing requirements, and integrate test systems with computer software for advanced data analysis.
The cost-effectiveness of digital instruments also played a significant role in their widespread adoption. As digital technology became more accessible and affordable, research institutions, industries, and laboratories could equip themselves with state-of-the-art test equipment without breaking their budgets.
Integration of Advanced Features
Innovation in digital test and measurement equipment didn’t stop at accuracy and efficiency improvements. Manufacturers began integrating additional features to further enhance usability and productivity. Modern digital instruments often come with built-in signal generators, enabling engineers to generate and analyze signals without the need for external devices.
Automation became a prevalent aspect of digital test systems. Engineers could program automated test sequences, reducing manual intervention and saving time during repetitive testing processes. Remote monitoring capabilities also emerged, allowing engineers to monitor and control instruments from a distance, streamlining operations in distributed setups.
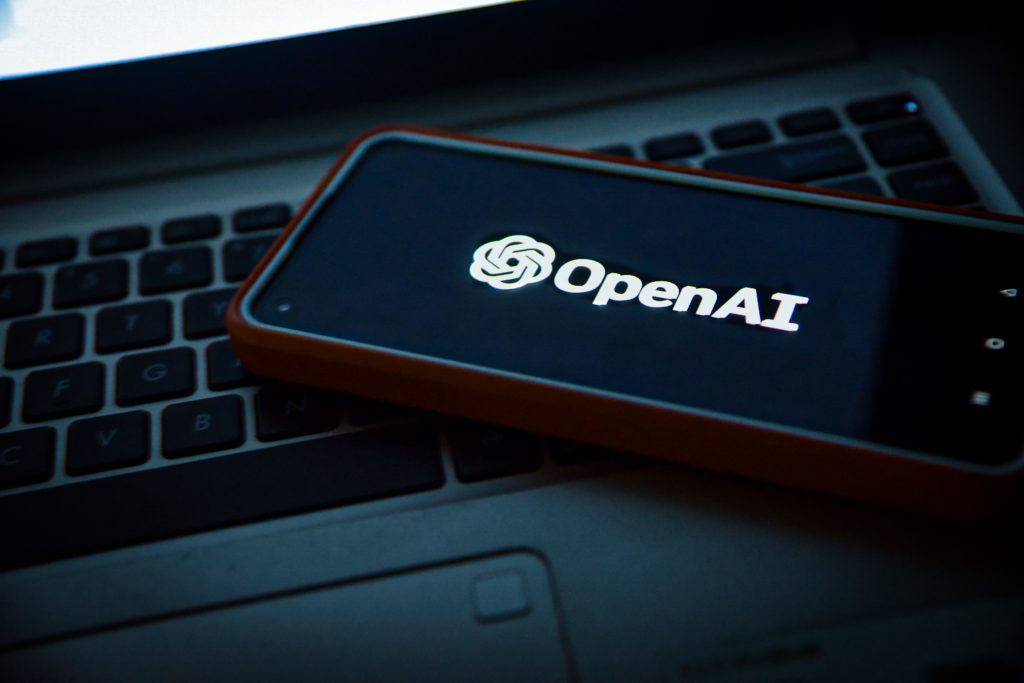
The test and measurement industry is continually evolving, embracing the latest technological trends. Artificial intelligence (AI) and machine learning are finding their way into test equipment, enabling intelligent analysis and pattern recognition. AI-powered instruments can autonomously detect anomalies, predict failures, and optimize test procedures.
Moreover, the Internet of Things (IoT) is transforming how test equipment interacts with other devices and systems. IoT connectivity enables remote data access, real-time monitoring, and cloud-based storage of test results, making collaboration and data sharing seamless.
The Future of Test and Measurement
As technology continues to advance, the future of test and measurement equipment holds immense promise. With the ongoing convergence of various cutting-edge technologies, we can expect even more sophisticated, versatile, and intelligent instruments. Advanced materials, nanotechnology, and quantum computing might pave the way for entirely new classes of test equipment, offering capabilities beyond our current imagination.
The journey from analog to digital test and measurement equipment has been transformative, driving progress and efficiency in various industries. Digital technology has revolutionized the accuracy, stability, and flexibility of these instruments- empowering engineers, researchers, and technicians to achieve unprecedented levels of precision in their work.